SaaS & PaaS role in Manufacturing Industries
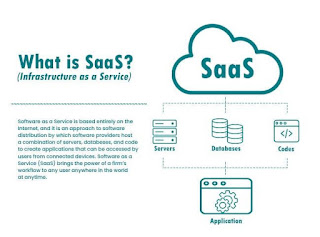
SaaS- Software as a Service : It is a type of model where a software is delivered as a license on a subscription basis. SaaS became a common delivery model for many business applications, including office software , messaging software , payroll processing software, DBMS software , management software, CAD software , development software, gamification , virtualization , accounting , collaboration , customer relationship management (CRM), management information systems (MIS), enterprise resource planning (ERP) , invoicing, field service management, human resource management (HRM), talent acquisition , learning management systems , content management (CM), geographic information systems (GIS), and service desk management . Some of the examples in manufacturing industries are CAD softwares for desiging & detailing of drawings, CRM software, ...